SUSPENSION
SUSPENSION SYSTEM
- Parts which are performing the function of isolating the automobile from road shocks(which may be in the form of bounce, pitch, roll or yaw) are collectively called as suspension system.
- The suspension system of an automobile is one which separates the wheel/axle Assembly from the body and also maintain the contact between tyre and road surface.
- It consists of spring and damper.
Objectives of Suspension system
- Prevent the road shocks being transmitted to the vehicle components.
- To prevent the occupants from road shocks and to give a comfortable ride.
- To make sure the stability of the vehicle during pitching, rolling and yawing motions.
1.Vertical loading
During bump or pit, it is subjected to tensile compressive and bending loads. These are observed by the elastic compression, shear, bending or twisting of the spring.
The front springing system should vibrate with less frequency than rear springs.
2.Rolling
During cornering, the center of gravity of the vehicle will be shifted outwards of the vehicle due to centrifugal force and road resistance acts inward at the wheels. This causes rolling about the longitudinal axis. This is checked by means of stabilizer.
3.Brake dip and squat
During braking and acceleration front of the vehicle will be lowered(dip) or lifted(squat). This is absorbed by providing radius rods.
4.Side thrust
During cornering cross-winds, cornering force or irregular load causes side thrust. This is absorbed by leaf springs or panhard rods.
5.Road holding
maintain the vehicle’s contact with the road surface during dip, squat, cornering..etc and in a straight line motion is called road holding. This is improved by avoiding weight transfer from front to rear or rear to front or side to side.
6.Ride and handling
To provide smooth and comfortable drive on a bumpy road. Handling is the ability to brake, corner and accelerate safely.
7.Unsprung weight
To reduce un-sprung weight (rear axle assembly, steering knuckle, wheels, tyres and brakes)
Elements of suspension system
1. Springs
It absorbs road shocks or impacts due to bump in road by oscillation.(Tyres also provides spring effect , but to a smaller extent).
2. Damper(shock absorbers)
They reduce the tendency of the carriage unit to continue to bounce up and down on its springs .
Oscillation due to road shocks are restricted to a reasonable level by damper.
Types of Suspension springs
Based on the material used
1. Steel spring
i) Leaf spring
ii) Tapered leaf spring
iii) Coil spring
iv) Torsion bar
2. Rubber spring
i) Compression spring
ii) Compression shear spring
iii) Steel reinforced spring
iv) Progressive spring
v) Face-shear spring
vi) Torsional shear spring
3. Plastic spring
Based on the working medium
1. Air spring
2. Hydraulic spring
Leaf spring
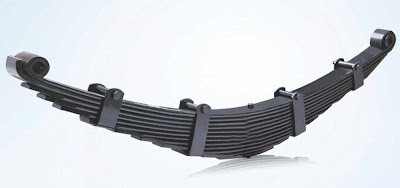

Leaf spring is the simplest type of suspension spring, commonly used in heavy and light duty vehicles. It is also known as flat spring made out of flat plates. It is designed as multi-leaf or mono leaf springs.




Types of leaf springs
Semi-elliptic is commonly used in cars and heavy vehicles. In transverse springs vehicle body will tend to roll in sharp corners.
- No of blades required are more while increasing the load. This adds more weight.
- Internal friction between the blades causes wear in springs.
- Internal friction causes squeaking sound.
- Occupy more space.
- Collection of moisture between the blades leads to rust formation.

- Helper springs are used only in rear side for wide range of loading.
- If the load is exceeding it will come into operation to share the extra load.
- Brackets are provided to stop the springs from over deflection.
Materials(Leaf spring)

Fibre composite leaf springs


- Its made of fibre-glass, laminated and bonded together by tough polyester resins.
- 3 to 5 times lighter than metallic leaf springs due to which less unsprung-weight.
- No squeaking sound
- No friction involved which leads to lesser wear.
- No sagging with time.
- laminated structure protects it from sudden spring-failure.
ii)Tapered leaf spring
Number of plates are bound together and heated to suitable temperature. Then inserted into roll-forging machine to get as a single unit in a desired shape and size.

Advantages over Conventional spring:
- Light weight (60% of conventional spring)
- No inter-leaf friction
- Absence of squeaking sound
- Stress are more uniform, this gives longer life.
- Occupy less space
- No moisture problem
Used in : Trains, Corvette C5



- Coil springs are used in conventional rigid axle suspension but mainly with independent suspension.
- It can be used in very congested space.
- Energy stored per unit volume is higher than leaf spring.
- No static friction.
- It produces no noise.
- It can take shear and bending stress.
- It can be used along with leaf spring.
- It cannot take side thrust and torque reactions.
Torsion bar

- Torsion bar is used in independent suspension system to take shear stress and is made of heat-treated alloy spring steel.
- Energy stored per unit weight of this material is nearly same as coil springs.
- Torsion bar acts as a spring when wheel hits a bump.
- The springing depends on the length and diameter of the rod.
- Up and down movement of the suspension system twists the torsion bar. It will then try to return to its original shape, moving the control arm to its original place.
- It Occupies less space.
- We can use hollow tube instead of solid one but with less stiffness.


Dis-advantages:
- It does not take braking torque and driving thrust.
- It can’t act as a damper.
Rubber springs
Rubber springs are used as bumping and rebound stops. When a suspension springs reaches its limit of travel, these prevents the metal-metal contact.
Advantages:
- It can store greater energy per unit weight than steel springs.
- It has good damping properties.
- No squeaking sound.
- More reliable.
- It doesn’t require lubricant.
- It is more reliable and simple construction.
- It can resist a load in large magnitudes.
- However it’s use is limited because a mechanical guide must be provided with this.



2.Compression-shear spring:
- The load is carried partly by shear and partly by compression.
- Large strains can be allowed in the body.


3.Steel-reinforced spring:

- Steel helical spring bonded in the rubber body.
- It has greater stroke/diameter ratio and used without any mechanical guide.

- It consists of a thick disc rubber having metal plates bounded on it’s flat surfaces and axially pre-compressed.
- It operates about the axis and takes shear load.

- It consists of an inner metal shaft(solid or tube) an outer trough-like shell between which rubber body is bonded and outer shell is fixed in the base plate.
- It can take shear loads.
- A shock absorber (dampers) is a mechanical or hydraulic device made to absorb and damp road shocks.
- A springing device must be compromise between flexibility and stiffness. It does this by converting the kinetic energy of the shock into another form of energy (typically heat) which is then dissipated to atmosphere. It can’t absorb but convert the form.
Types:
1. Friction type
It is obsolete now due to it’s non-predictable damping characteristics.
2.Hydraulic type


The principle of operation is when a piston forces the fluid in the cylinder to pass through a hole, a high resistance to the movement of piston is developed which provides the damping effect.
Derived its name from the tubular shape of telescopes.

1.Mono tube
2.Twin tube

Construction
Rod G is aatched to the two way valve A, while another similar valve B is attached to the lower end of cylinder C. There is a fluid in the space below the valve A and below the valve B and also in the space between cylinder C and tube D. The oil is a mixture of transformer oil(60%) and turbine oil(40%).H is the gland in the head J and any fluid scrapped off by the rod G is brought down into the annular space through the inclined passage on the head. The eye E is connected to the axle, while eye F is attached to frame.
Working:
When a vehicle has come across a bump, eye E would move up and thereby the fluid will pass from the lower side of valve assembly A to its upper side. Since the volume above A is reduced by the rod G, the fluid will also exert its pressure on the valve assembly B and go to the underside of valve B. This passing of the fluid through valve openings provides the damping. Similarly for downward motion of the eye E during rebound, the fluid will pass from the upper side of the valve assembly A to the lower side and also from the lower side of the valve assembly B to its upper side.
Disadvantage:
The turbulence of fluid causes air in the tube to mix with the fluid which reduces the viscosity of the fluid which leads to reduced shock absorber control. To overcome this problem inert gas(Nitrogen) is used as working medium along with hydraulic oil (SAE 10W to SAE 30W) with a pressure between (2.5 bar to 30 bar). (gas is used to reduce the tendency for the oil to cavitate under heavy use).
Mono tube shock absorber:
Mono tube type is similar to the twin-tube type except that there is a single tube with piston inside.
The piston has two valve in it, one opens during bump, while the other opens during rebound. Modern shock absorbers are velocity-sensitive. Double acting shock absorbers offer resistance both during compression and rebound of the springs.


It is an air inflatable shock absorber, to bring back the car back to the level when the load is down by inflating the air. It is similar to the standard shock absorber, except that these have an air chamber bladder which forces apart the upper and lower sections of the shock absorber, which increases the distance between the axle and the vehicle body. Inflating of air is either done either from garage air line or by pumping system linked to the car engine. Both the rear units are connected with a high pressure hose. In case of failure of the air circuit, it behaves as an ordinary shock absorber.
Telescopic type shock absorber
Shock absorber ratio:
It is the ratio of resistance to upward movement and resistance to downward movement. Most of the shock absorbers are designed for 50/50 ratio.
Electronically controlled (EC) shock absorber
This allows the driver to select the amount of damping electronically. It is achieved by varying the size of valve’s orifices. This assembly consists of electric motor, control rod. This is done manually or automatically by a computer-controlled system activates according to the input from various sensors.

Types of suspension system
1.Rigid axle (or) solid axle (or) dependent suspension system
2.Independent suspension

1.Rigid axle / Non-independent suspension:
When one wheel hits a bump in the road, its upward movement causes a slight tilt of the other wheel.
This causes the whole of the wheel to tilt on one side and wheel starts to wobble.
Road adhesion is also decreased.
2.Independent suspension
It allows one wheel to move up and down with minimal effect or no effect to the other.
Advantages
- Elastic strain energy per unit spring weight stored in a coil or torsion bar is greater than conventional leaf spring.
- Unsprung weight is reduced which reduces the scrub.
- Soft springs provide better riding comfort.
- Improved steering precision since wheels are not inter-linked.
- Absence of solid axle, engine position can be moved forward and downward which results in more passenger space.
1.High initial cost.
2.Greater maintenance required.
3.More rigid frame or sub-frame is required in the absence of rigid axle.
FRONT(LIVE) AXLE SUSPENSION SYSTEMS:
- Wishbone type
- Mac person strut type
- Vertical guide type
- Swinging half-axle type
1.Wishbone type or parallel link type
Type of double-A or double wishbone suspension as the arms resembles the letter ‘A’. Although the lower arm in these systems can sometimes be replaced with a single solid arm. The spring is placed between the lower wishbone and the underside of the cross member. The shape ‘V’ of the arms restrict acceleration, braking and cornering forces.
The vehicle weight is transmitted from body and cross member to the coil springs through which it goes to the lower wishbone member.

Between the outboard end of the arms is a knuckle. The knuckle contains a kingpin for horizontal radial movement in older designs, and rubber or trunion bushings for vertical hinged movement. In newer designs, a ball joint at each end allow for all movement. A damper is placed inside the coil springs. The unequal arm helps to keep the contact patch square on the ground, increasing the ultimate cornering capacity of the vehicle.
This suspension can take vehicle weight, cornering forces and braking torque. But spring movement causes a change in camber angle which leads to better handling.
Disadvantages
- Occupies more space consuming the boot space for the passenger.
- Design process is little complicated and costlier.

wishbone type used with anti-roll
bar

2.Mac person strut type

It resists braking, side and accelerating forces. It is simpler than double wishbone, lighter and less unsprung weight. No change in camber angle during up and down movement of wheel. This type of suspension gives the maximum room in the engine compartment, therefore, commonly used on front wheel drive cars. Stabilizer bar can be used along with suspension.


Used in: Maruti 800, VW Jetta, MS Swift dzire, Hyundai i20, Volkswagen Polo, XUV 500
The since the structs (shock absorbers) are almost vertical, the ride height is high causing the CG of vehicle to rise.

Kingpin is directly attached with cross member of frame. It can slide up and down corresponding to the wheel motion. Wheel track, wheel base remains unchanged. But this system having the disadvantage of decreased stability.
4.Swinging half axle suspension
Wheels are rigidly mounted on the half axles which are mounted to the chassis at other end.
Camber angle varies due to the up and down movement of the wheels.
Rear axle(live axle) Independent Suspension systems



1.Multilink suspension
2.De-dion suspension
3.Trailing arm suspension
4.Semi trailing link suspension
5.Transverse suspension system
1.De-dion suspension

It is used in both dead axle and live axle. De Dion suspension uses universal joints at both the wheel hubs and differential end.
Used in : Porsche Spyder replica
2.Trailing arm suspension



Trailing links are pivoted at right angles to the longitudinal axis of the car(ahead of the axle)and carry the rear wheels at the other end. Coil springs and dampers are attached with the trailing link.
It absorbs accelerating and braking forces. During acceleration and braking, trailing arm movement changes the wheel base. Torsion bar can be used along with trailing arm.
Used in: Renault 4, 5, Citroën 2CV, Renault Duster.
3.Semi-trailing link

Trailing arms are inclined from 20deg to 40deg with the longitudinal axis. Camber angle changes due to the up and down movement of the wheels. Increased cargo room in the rear but more unsprung weight leads to poor ride quality.
Used in: Airplane landing gears
4.Transverse suspension system

It is used in both front and rear suspension. Combines independent double wishbone suspension with a leaf spring. It involves one leaf spring mounted across the vehicle, connected at each end to the lower wishbone. The center of the spring is connected to the front sub frame in the middle of the car.
There are still two shock absorbers, mounted one to each side on the lower wishbones.
Used in: Ford Model T(solid front axle), corvette C5 and C6
5. Multilink suspension

The basic principle of it is the same as wishbone, but instead of solid upper and lower wishbones, each 'arm' of the wishbone is a separate item. These are joined at the top and bottom of the spindle thus forming the wishbone shape. As the spindle turns for steering, it alters the geometry of the suspension by torqueing all four suspension arms. Spring is installed separately from the shock absorber. it's also a very good for off road driving. The multi-link suspension uses three or more lateral arms.

Used in: Audi A4,A8, Audi A3 Cabriolet, Mazda RX-8, Jaguar XE, MS Grand Vitara,Tesla model 3
Anti-Roll bar

It is also known as Stabilizer Bar and sway bar. It is an U-shaped stabilizer bar is having two rubber bushings mounted by metal brackets in the axle and its also connected with the chassis frame at two points. As the name implies the function of a sway bar is usually to prevent the vehicle from rolling. Its preventing weight transfer from one side to the other in cornering situations it is acting as a torsion bar.
The inside wheel in a corner maintains more of its static weight. It’s main function is to equalize the level of suspension springs during cornering.
AIR SUSPENSION
It is also known as inter-connected suspension system. In these systems, the front and rear suspension units or else the units on the two sides of the vehicle are connected together. It Comprises of compressor for supplying air to air tank and air bag which replaces coil spring and is made of composite of textile re-inforced rubber and polyurethane, which provides structural integrity, air-tight construction, toughness against light abrasion from road debris and sand, and resistance to salt and chemical corrosion.
Compressors can be activated manually or automatically, and controlled solely by the driver, automatically through an electronic system, or a combination of both. The drier uses a substance known as a desiccant to absorb as much moisture from the air as possible before the air is sent through the system. Pressure maintained about – 5.6 to 7 kg/ sq.m or 240MPa.
Air bags – on each wheel in the place of coil springs. As load applied, air bags compressed actuating the levelling valve. Initially, each left and right air bag was connected by a line and shared air. As the vehicle cornered, one air bag compressed its air and pushed it through the line to the other air bag, which was expanding. This resulted in severe body roll. Now, systems use a levelling valves that control this tendency and offer bettering handling. Solenoids are used in electronically-controlled systems to fill and vent each air bag. As the system adjusts for different conditions, it commands each solenoid to open or close, changing the amount of air in each of the bags.
Electronic systems are managed through an electronic control unit. The controlling software monitors the pressure and ride height in real time. The modules receive information through a variety of inputs, including ride-height sensors, and toggle the compressor on and off as needed.Some high-end cars with air suspension even combine GPS and map data to automatically adjust the car’s suspension settings in anticipation of the next corner on the route.
Used in: Volvo Buses, Daimler Setra Evo bus, Mercedes C-Class, Audi A6, Audi Q7, Rolls-Royce Phantom
Types:
![]() |
Piston type |
![]() |
Bellow type |
![]() | |
|
Types of system:
1.Pressure based system
Monitor only the air pressure in the bag.
2.Ride-height system
Monitor how much a car raises and lowers while monitoring the pressure needed to reach each level.
Advantages of air suspension:
- These maintain a constant frequency of vibration whether the vehicle is laden or unladen.
- Constant frame height is maintained which avoids the change of head lamp alignment.
- It can provide about three times softer ride than coil springs.
- It helps to reduce the load while the vehicle is in motion i.e. the dynamic loading as the spring rate variation between laden and unladen weight is much less.
- It gives smooth and comfort ride of the vehicle and noise reduction.
Air bag or air strut failure - due to old age, or moisture within the air system that damages them from the inside.
Compressor failure - Compressor burnout may also be caused by moisture from within the air system coming into contact with its electronic parts.
Dryer failure - which functions to remove moisture from the air system eventually becomes saturated and unable to perform that function
Hydro-elastic Suspension
A system where the front and rear suspension systems were connected together in order to maintain the level of the car when driving. The front and rear suspension units have Hydrolastic displacers, one per side. These are interconnected by a small bore pipe. Each displacer incorporates a rubber spring. Damping of the system is achieved by rubber valves.


Hydro gas(hydro-pneumatic) suspension
The difference between the hydro-gas and hydro-lastic suspension is in the displacer unit .
In the Hydrolastic system, fluid was used in the displacer units with a rubber spring cushion built-in. With the Hydrogas, the rubber spring is removed completely. The fluid still exists but above the fluid there is now a separating membrane or diaphragm, and above that is a cylinder or sphere which is charged with nitrogen gas. The nitrogen section is what has become the spring and damping unit while the fluid is still free to run from the front to the rear units and back.

Renault duster shock absorbers
ReplyDeleteRenault Kwid shock absorbers
Renault duster shockers
Renault kwid shockers
Nice Post. Thanks for Sharing
ReplyDeleteAutomobile Suspension Part Manufacturers in India
suspension parts manufacturers in India
Best Automobile Part Manufacturers in India
Shock Absorber Manufacturers in India
Brake Shoe Manufacturers in India
Brake Manufacturers in India
Car Suspension Parts Manufacturers in India