WHEELS AND TYRES
Wheels
A wheel is a circular block of a hard and durable material at whose center has been bored a circular hole through which is placed an axle bearing about which the wheel rotates when a moment is applied by gravity or torque to the wheel about its axis.
A tire is the rubber part of a wheel that grips the road. The wheel, along with the tyre has to take the vehicle load, provide cushioning effect and cope with the steering control.
Requirements of Wheels:
- It should be balanced both statically as well as dynamically.
- It should be lightest as possible to reduce the unsprung weight.
- It should be possible to remove and mount the wheel easily.
- Its material should not deteriorate with weathering and age.
Types of Wheels:
- Pressed steel wheel
- Wire wheel
- Alloy wheel
1.Pressed steel wheel:
- This wheel is used over 90 % of world manufacturers worldwide because of its simplicity, robust construction, low cost manufacture, mostly used in heavy vehicles.
- This type consists of two parts, a steel rim to accommodate the tyre and a pressed steel disc.
- The rim and disc may integral or permanently attached.
- The rim profile(tyre bead profile) indicated by letters J, K, JJ, JK or B in the specification.
- WELL is used for removing and mounting the tyre easily.
- Rim seat has 5 to 15 degree taper so that as the tyre is inflated, the beads are forced up taper to give wedge fit and makes a good seal.
- The Steel disc performs the function of the spokes.
- Holes are provided in the disc for ventilation and cooling of brake drum.
- A hole in the rim is used to accommodate the tube valve.
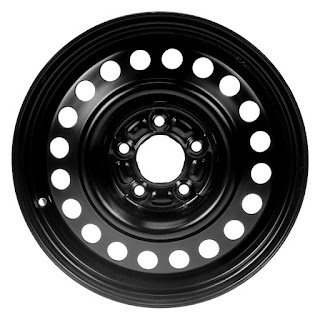


Based on the position of the rim in relation to attachment face of the disc
1. Inset or positive offset wheel
- The center line of the rim is located inboard of the attachment face of the disc.
- Inset is the distance from the attachment face of the disc to the center line of the rim.
- Mounting face of the disc is located inside.
- To provide a wider wheel base for better stability, or to allow installation of wide wheels and tires without interfering with inboard chassis or suspension parts.
- Found in front wheel drive cars.
- Cornering forces can be more effectively coped with by the outside tyres.


2. Zeroset wheel
- The center line of the rim and the attachment face of the disc are lying in the same line.
- Least stress on wheel on bumpy roads.
3. Outset or negative offset wheel
- The center line of the rim is located outboard of the attachment face of the disc.
- Mounting face of the disc is located inside.
- This wheel type has less wheel track.
Reversible wheel: A wheel whose disc can be mounted on either face to provide inset, outset and Zeroset.
Divided wheel: A wheel constructed in two parts, which when securely fastened together combine to form a rim having two fixed flanges is called a divided wheel.


2.Wire wheels
- it is the earliest type of wheel but it’s use is limited to vintage sports, racing cars and two wheelers.
- It is lighter, better heat dissipation for brake drum and can be fitted and removed easily as only one nut has to be removed.
- The spokes are attached to the rim on one end and pushed through a hole in the wheel rim on the other end.
- Spokes are screwed down by nipple, pulling the spoke tightly.
- Spokes are mounted in criss-cross manner.
- The spokes carry the weight, transmit the driving and braking torque and withstand side forces while cornering, but it can’t take compressive or bending stress.
- As rim has a holes, tubeless tires can’t fit into these wheels.

![]() |
Spokes transmitting driving torque
|
![]() |
Spokes taking the braking torque
|
![]() |
Spokes
carrying weight
|
![]() |
Spokes
taking side thrust
|
3.Alloy wheel

- This is the most recent type automobile wheels in use, especially in cars and two wheelers.
- It is made of aluminium or magnesium alloys.
- It weighs about 50% of the steel wheel for the same strength and also alloys are best heat conductors which helps the heat dissipation.
- Magnesium alloys have high impact and fatigue strength so that they can stand vibrations and shock.
- Generally aluminium alloy wheels are used for cars and commercial vehicles while magnesium alloy wheels are used by sports cars.
- It has low aspect ratio which gives stability on cornering.
Wheel Dimensions

W-Width of wheel(inches or millimeters)
D-Diameter of wheel(inches or millimeters)
C-Offset
Example 6 B 13 , 4 J-14

TYRES


- Tyre is a rubber member which gives the cushion to the automobile. It consists of outer cover i.e. tyre and tube inside.
- The tyre-tube assembly is mounted over the wheel rim and air inside the tube carries entire load and provides cushioning effect.
Functions of tyre:
- To support the vehicle load.
- To provide cushion against the road shocks.
- To transmit driving and braking forces to the road.
- To provide cornering power for smooth steering.
Tyre cross-section:


Properties of tyre:
Non-skidding
The tread pattern must be designed to permit least amount of skidding even on wet roads.
Uniform wear
The tyre wear must be less and uniform in order to maintain the non-skidding property.
Load-carrying
The tyre material and design must be able to ensure that the tyre is able to sustain the stresses due to revolution.
Cushioning
The tyre should be able to absorb high frequency vibrations imparted by road surface and provide cushioning effect.
Power consumption
The tyre absorb some power due to the friction between the tread rubber and road surface and also due to hysteresis loss(as heat).
Tyre noise
The tyre noise should be minimum when rolling.
Balancing
The tyre must be balanced statically as well as dynamically.
Types of Tyres:
The pneumatic tyres are classified according of following considerations
1.Basic construction
2.Use
3.Ability to run flat
Basis construction:
1.Conventional tubed tyre
2.Tubeless tyre
1.Conventional tubed tyre:

Plies – Layers of strong fabric which are built up to give the tyre its strength and shape.
Its made of rayon material.
Tube - Which contains air under pressure. A non return valve is attached with it. It is made of Butyl Rubber.

Bead – Two rings that are made of steel wire and encased in rubber. They hold tire side walls snugly against the rim and prevent tyre from coming off.
Tread – Rubber pattern Outer surface of the tyre that comes in contact with the road.

Side Wall – The sidewall is that part of the tire that bridges between the tread and bead. The sidewall is largely rubber but reinforced with fabric or steel cords that provide for tensile strength and flexibility.
Breaker strip- A strip of fabric under the tread of a pneumatic tire casing, designed to protect the carcass.
Shoulder- The tire shoulder offers support and protection to both the sidewall and the tread. The shoulder is one of the thickest parts of the tire, enabling the tire to more easily hold its form during cornering maneuvers.
Filler(apex)- The apex provides a cushion between the rigid bead and the flexible inner liner and body ply assembly.
Tubeless tyre

- Tubeless tyre does not need a separate tube, instead air under pressure is filled inside the tyre.
- The construction of tubeless tyre is almost same as tubed tyre, except that it is lined with special air-retaining liner made up of a halogenated chlorobutyl or bromobutyl for better air impermeability with high heat and weather resistance.
Advantages of tubeless tyres
- Lesser unsprung weight.
- Better cooling.
- Slower leakage of air.
- Simpler assembly.
- Improved safety.
2.Based on usage
1.All weather tyres
- These are commonly found on almost all production cars.
- They are made of hard rubber for longer life which decreases grip and cornering power.
2.Summer tyres
- In these tyres, performance and grip are preferred over tyre life so made of soft rubber.
- Tread design is such way that it provides better grip, but less ability to remove water on wet roads. Summer tyres have fewer sipes than winter tyres.
3.Snow/ice tyres
- These have larger tread block patterns, which creates much noise.
- Snow tyres have small metal stud inserts which bite into the snow and ice.
- These tyres have a short life if run over dry roads.
4.Wet-weather tyres
- Tread design is such way that to disperse water from the contact patch.
- It is made of soft rubber, their life is 50% less than all-season tyres.
5.All-terrain tyres
- These are commonly used on SUVs and pick-up trucks for off-road conditions.
- These are larger in size and have stiffer sidewalls and bigger tread-block patterns.
- These tyres are noisy.
3.Ability to run flat
Flat running tyres are designed to resist the effects of deflation and to enable the vehicle to drive continuously after the puncture, at reasonable speed, so this would avoid accident due to sudden puncture and will allow the driver to reach the repair shop without changing the tyre.
1.Self-sealing tyres
This tyre has just the standard construction except that there is an extra lining under the tread area and is coated with puncture sealant which can seal punctures up to 4mm in diameter.
These days sealant can be injected through air valve of ordinary tyre. The centrifugal force due to rotation distributes the sealant uniformly over inner surface, forming a lining which serves as a sealer.

2.Self-supporting tyres
- These tyres are constructed in such a way that the side walls are more stiff and can support the vehicle weight by themselves in case of puncture.


- Rubber sandwiches the layers heat-resistant cord in the side walls and have special beads which retain their grip over the rim in the event of air loss.
- These tyres should incorporate tyre pressure monitoring system to indicate the driver about the pressure loss.
- These tyres maintains vehicle stability for 80km at a speed up to 85kmph.
Types of carcass(Plies):
- Cross ply (or) bias ply type.
- Radial ply type.
- Belted bias ply type.
1.Cross ply (or) bias ply type

- One of the oldest design.
- The tire is constructed to form a single working unit.
- Nylon textile plies are laid across each other(30deg-40deg), running from bead to bead in alternate directions.
- Number of plies depends on the size of the tyre and the load it has to carry.
- Same number of plies is used on the crown and the sidewalls.
- It does not use belts but it has thicker sidewalls, which can improve sidewall cut resistance.
- It Allows body of the tyre to flex easily and Improved cushioning, hence smooth ride on rough roads.
- These tyre were used in classic cars.
Dis-advantages:
Reduced traction at high speeds(due to sidewall flexibility) and increase rolling resistance.
Two layers rubbing thus produce heat which would damage the tyre material.
2.Radial ply type:

- Plies run straight across from bead to bead. i.e in the direction of tyre axis.
- A radial tire is constructed in two parts. The casing has one layer of steel cables that form arc from one bead to the other. Then several rubber-coated steel plies make up reinforced with metal wire that are placed under the tread to stabilize the crown. These belts resist cuts and punctures.
- Each ply is laid at an angle of 90 degrees to the direction the tyre rolling
- Radial tires have a bigger footprint, stiffer tread and distribute weight in a more uniform manner thus provides directional stability.
Advantages:
- Its shock absorbing capacity is 25% more than bias ply.
- Lower rolling resistance and hysteresis loss leads to less fuel consumption.
- Larger resistance to punctures ,cuts and impacts in the tread area.
- Longer tread life because of less heat build up in tyre.
3.Belted bias ply:

- This is a combination of radial and bias ply.
- Bias ply tyres with belts added to increase tread stiffness.
- Belts do not run around the sidewalls, they lay under the tread area only
- Belts and plies run at different angles.
- Offers some reduction in rolling resistance over a bias ply tire
- The belts increase the resistance of the tyre to punctures.
- Provides smooth ride and good traction.

Hydroplaning(Aquaplaning)
- Hydroplaning is when a vehicle starts sliding uncontrollably due to the tires encountering more water than the treads can displace. When driving at high speeds over wet pavement, the water begins to push the front tires off the ground slightly, creating a thin film between the tire and the road. That film, and it results in separation of the road and tire, it results in loss of steering, braking and power control.
- Rubber tires have tread (grooves) that are designed to channel water from beneath the tire. This creates higher friction with the road surface and can help prevent or minimize instances of hydroplaning.


Tyre terms :
Aspect ratio:

- The aspect ratio of a tire is determined by dividing a tire's section height by its section width. This is described as a percentage of the tire width.
- Lower the aspect ratio, better load carrying capacity, less wear and higher cornering power.

Ply rating
The ply rating branded on a tire's sidewall identifies how much load the tire is designed to carry at its industry specified pressure.

154-width of tyre in mm
151-% of height (i.e height=(151/154)X100%)

![]() |
Tyre description
|
These tyres looking very high quality and i will surely try it for my car because i need to change my car tyres. cheapest tyre shop in abu dhabi
ReplyDeleteIf anyone looking for a quality collection of various premium and mid-range tyres should check Wheelworx Auto Studio. Get in touch with tyre specialists for quality and affordable tyres in Adelaide.
ReplyDeleteGreat article on wheels and tyres! Comprehensive and informative. It covers types and functions well, including aspects like balance, materials, and various tyre designs. Especially useful for anyone looking into wheel repair or upgrades.
ReplyDelete